What Is Safety Stock and Why Does It Matter in Retail?
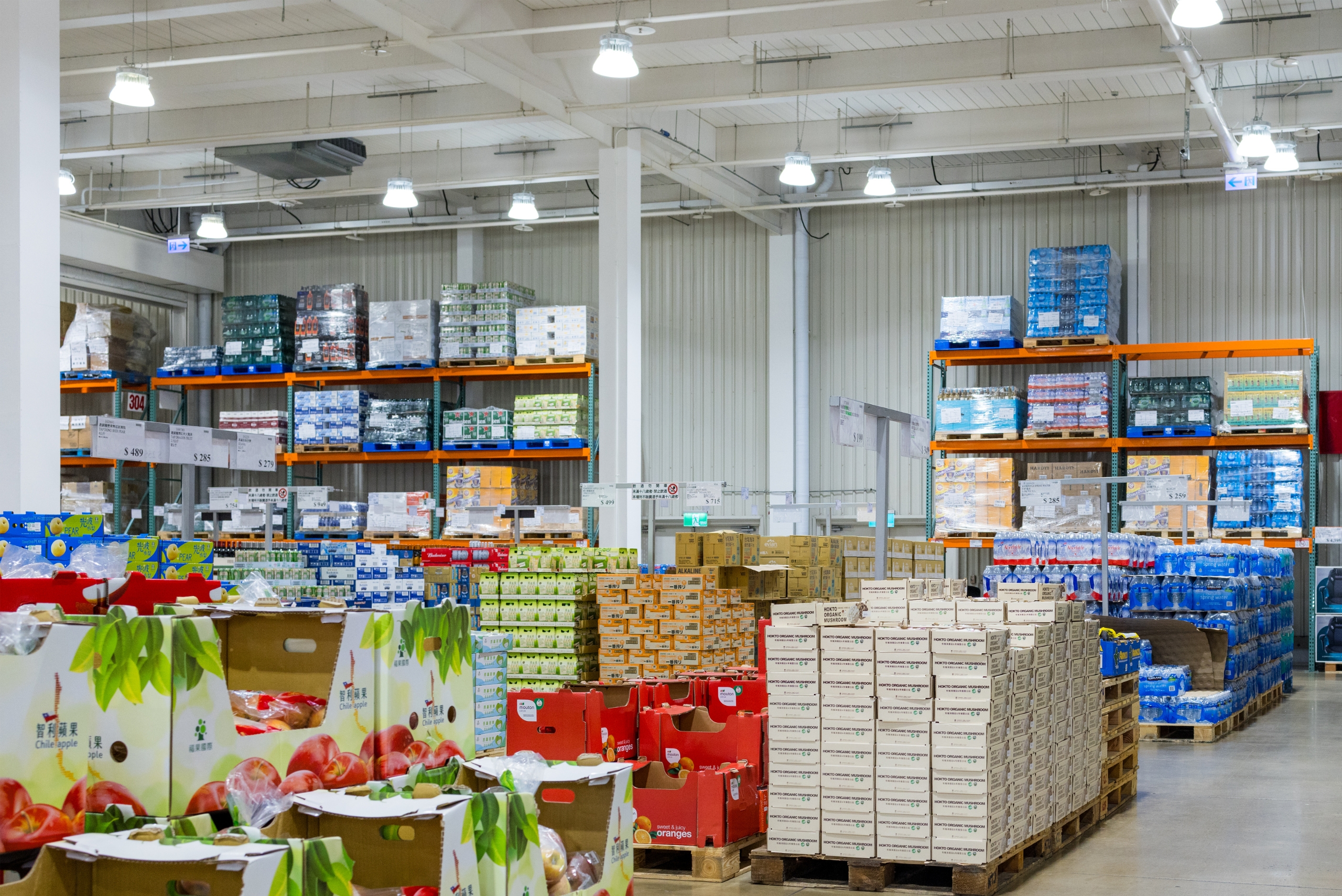
Poor stock management can lead to significant financial losses. When customers can’t find what they’re looking for, they are likely to turn to competitors, undermining the trust and brand reputation you’ve worked hard to establish. Fortunately, there are several supply planning strategies and tools to prevent stock shortages, including the determination of various stock levels, such as safety stock. This article delves into the concept of safety stock, its importance, and how to calculate it effectively.
Why You Need Safety Stock to Avoid Shortages
Businesses often face unforeseen challenges, such as:
- Sudden increases in customer demand,
- Delays in supplier deliveries,
- Product defects or deterioration,
- Loss, theft, or inventory errors.
To mitigate stock shortages, logistics managers can establish safety stock. But what is it exactly?
Safety stock, also referred to as buffer stock, is an additional quantity of inventory kept on hand to minimize the risk of stockouts due to unexpected demand or supply chain disruptions. It’s a critical metric for supermarkets, grocery stores, pharmacies, and virtually any other business.
However, it’s important to calculate safety stock accurately. Overestimating it can lead to overstocking, which ties up cash flow unnecessarily. Learning how to calculate it according to your business needs is essential.
How to Calculate the Right Safety Stock Level
Several methods have been developed for calculating safety stock. Let’s explore the most common ones:
Based on desired safety days
A straightforward method is to calculate safety stock based on the number of extra days of inventory you want to have on hand. For example:
If your average daily sales are 200 units and you want to maintain safety stock for 7 days, the calculation is:
SS = 200 × 7 = 1,400 units.
In simple terms:
Safety stock calculation formula = Average daily sales x Desired safety days |
You can then set an alert to reorder inventory at the right time by adding this safety stock to the product of delivery time (in days) multiplied by average daily sales.
Based on maximum variation
This method is more precise as it factors in variability in demand and lead times.
For instance, over a year:
- Average daily sales = 200 units,
- Maximum daily sales = 300 units,
- Average lead time = 10 days,
- Maximum lead time = 15 days.
The calculation is:
SS = Max Lead Time x Max Daily Sales - Avg Lead Time x Avg Daily Sales |
Substituting the values:
SS = (15 × 300) − (10 × 200) = 4,500 − 2,000 = 2,500 units.
This approach accounts for potential spikes in demand while avoiding excessive overstocking.
Based on normal distribution
If lead times are consistent or unknown, you can use the normal distribution formula (also known as King’s method):
SS = Service factor x Demand variance x √(Lead Time) |
- The service factor represents the desired service level, indicating the tolerance for stockouts.
- The demand variance reflects historical fluctuations in sales.
According to the ABC categorization method, focus should be placed on the top 20% of products that account for 80% of sales, as these have the greatest impact on customer satisfaction.
Leveraging artificial intelligence
Some advanced inventory management systems use artificial intelligence (AI) to predict demand. AI analyzes historical sales data as well as external factors such as weather or geopolitical events. This allows for real-time adjustments to safety stock, making it particularly useful for complex supply chains.
Optimizing safety stock management
To achieve optimal safety stock management, consider the following strategies:
Use inventory management software
Stock management software consolidates inventory data in one place, enabling accurate calculations for safety stock, minimum stock, seasonal stock, and other key metrics. These tools can also automate replenishment and provide insights into stock turnover rate.
Strengthen supplier relationships
Building trust and maintaining open communication with suppliers ensures more reliable lead times. A strong relationship makes it easier to resolve issues such as delayed shipments and allows for better visibility into production and shipping schedules.
Minimize shrinkage
Shrinkage, including theft, loss, or inventory errors, can distort calculations and lead to inaccurate stock levels. To combat shrinkage:
- Install security systems, such as video surveillance, to monitor inventory
- Train employees to handle stock carefully and identify potential theft
- Use RFID tags or barcodes to track products efficiently
Veesion leverages AI to enhance security and minimize shrinkage. Its software detects suspicious gestures in real-time, alerting managers via their smartphone or tablet to prevent theft. This proactive approach ensures that inventory levels remain accurate, reducing both stockouts and excess inventory.
Whether you run a small shop or a large retail chain, Veesion’s solutions can help safeguard your inventory and improve operational efficiency.
For more information, don’t hesitate to contact our team. Together, we’ll find solutions tailored to your business needs!
The most popular
Related news
Discover what Veesion can do for you. Do you have one or more stores?
Our team will contact you within 48 hours