What is minimum stock and what is it used for?
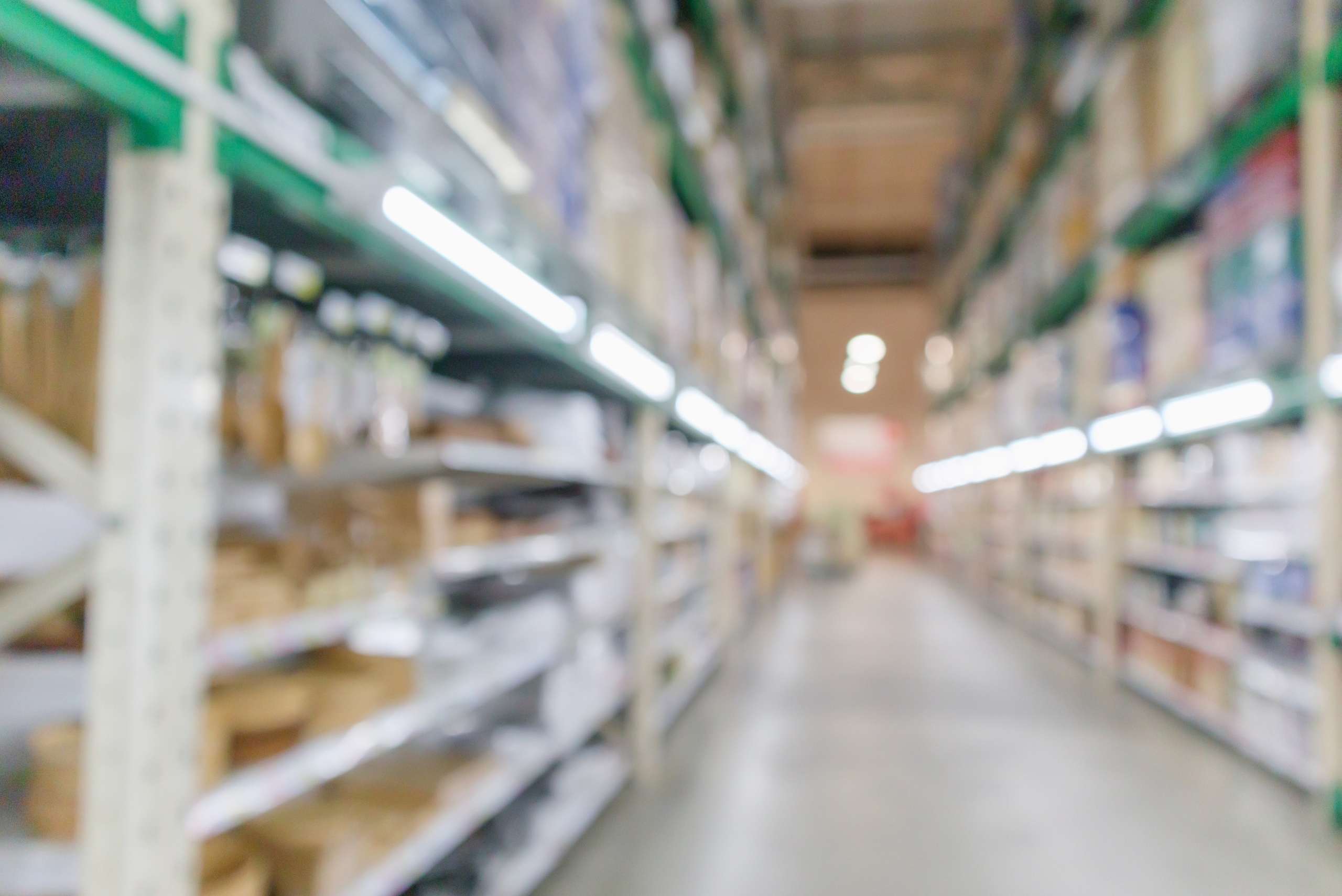
Minimum stock offers retailers and supermarket managers the ability to determine the stock level below which consumer demand can no longer be met. But what exactly does "minimum stock" mean, and how is it calculated? Let’s dive into this essential concept for preventing stockouts and ensuring customer satisfaction.
What is minimum stock for?
Minimum stock levels are invaluable for managing store inventory. This represents the number of items that must be in stock to meet customer demand, even during restocking periods.
Additionally, it serves as a basis for determining other stock levels, including safety stock and alert stock.
How to calculate minimum stock levels?
To calculate minimum stock levels, you need to know :
- The quantity of products sold over a specific period ;
- The replenishment lead time.
For example, for a given product:
- 20 units are sold weekly ;
- The delivery time is two weeks.
To calculate, determine the average daily sales rate:
- Approximately 2.86 units sold per day.
- 14 days of delivery time.
Then, multiply the two: 2.86 × 14 = approximately 40. Therefore, the minimum stock level for this product is 40 units.
Formula Minimum stock= D (Delivery time in days) x Q (Quantity consumed per day). |
How to calculate other stock levels from minimum stock?
Once the minimum stock for an item is established, you can calculate safety stock and alert stock levels.
Safety stock
Safety stock, or buffer stock, is the quantity of products needed to meet consumer demand under unforeseen circumstances, such as unexpected surges in activity, supplier issues, delivery delays, or other disruptions.
Safety stock is calculated based on how many extra days of inventory you want to have on hand. For example, if 20 units of a product are sold daily, and you want 7 days of buffer, the calculation is:
20 × 7 = 140 units.
Alternatively, for greater precision, use the formula:
Safety Stock = (Maximum daily sales × Maximum lead time) − Minimum Stock.
For instance, if:
- Maximum daily sales are 20 units.
- Maximum lead time is 20 days.
- Minimum stock is 40 units.
The calculation would be: 20 × 20 − 40 = 360. Using this method, the safety stock is 360 units.
Alert stock
Alert stock is a predefined threshold that signals when it’s time to place a new order to prevent stockouts.
The formula is:
Alert Stock = Minimum Stock + Safety Stock.
Which products require minimum stock levels?
While minimum stock levels apply to all products, they are especially critical for the 20% of items that account for 80% of stock value, according to the ABC method or Pareto Principle.
- Category A products (high-priority, high-value) require the closest monitoring.
- Category B products (moderate value and priority) need less vigilance.
- Category C products (low value, low priority) can have reduced safety stock levels to avoid tying up funds unnecessarily.
Please note that, for perishable products, it is important not to set the safety stock too high, otherwise you run the risk of overstocking and having to throw them away. In this case, it is essential to calculate the stock turnover rate.
How to optimize minimum stock management?
Technology offers the best solutions for optimizing minimum stock management. Here are some tools to consider:
- An inventory management system (IMS) : These systems centralize inventory data, providing real-time information on minimum stock, safety stock, and alert stock levels. Many systems can even automate order placement.
- Data analysis software : Using historical data and advanced algorithms, these tools forecast demand and adjust stock levels accordingly. Artificial intelligence is often employed to enhance accuracy for large datasets.
- Bar codes, RFID tags and sensors : These technologies simplify inventory management. Barcodes streamline inventory counts, while RFID tags allow for remote identification of items, improving efficiency.
- A shop video surveillance system : These systems help manage shrinkage (employee or customer theft) to ensure stock data aligns with actual inventory levels.
At Veesion, our advanced technology complements inventory management systems by detecting suspicious behaviors that may indicate theft attempts. Our software enhances stock management by providing real-time alerts, enabling store managers and employees to take swift action to prevent losses. This ensures stock levels remain optimal, minimizing stockouts and securing inventory.
The most popular
Related news
Discover what Veesion can do for you. Do you have one or more stores?
Our team will contact you within 48 hours