What are the different types of stock?
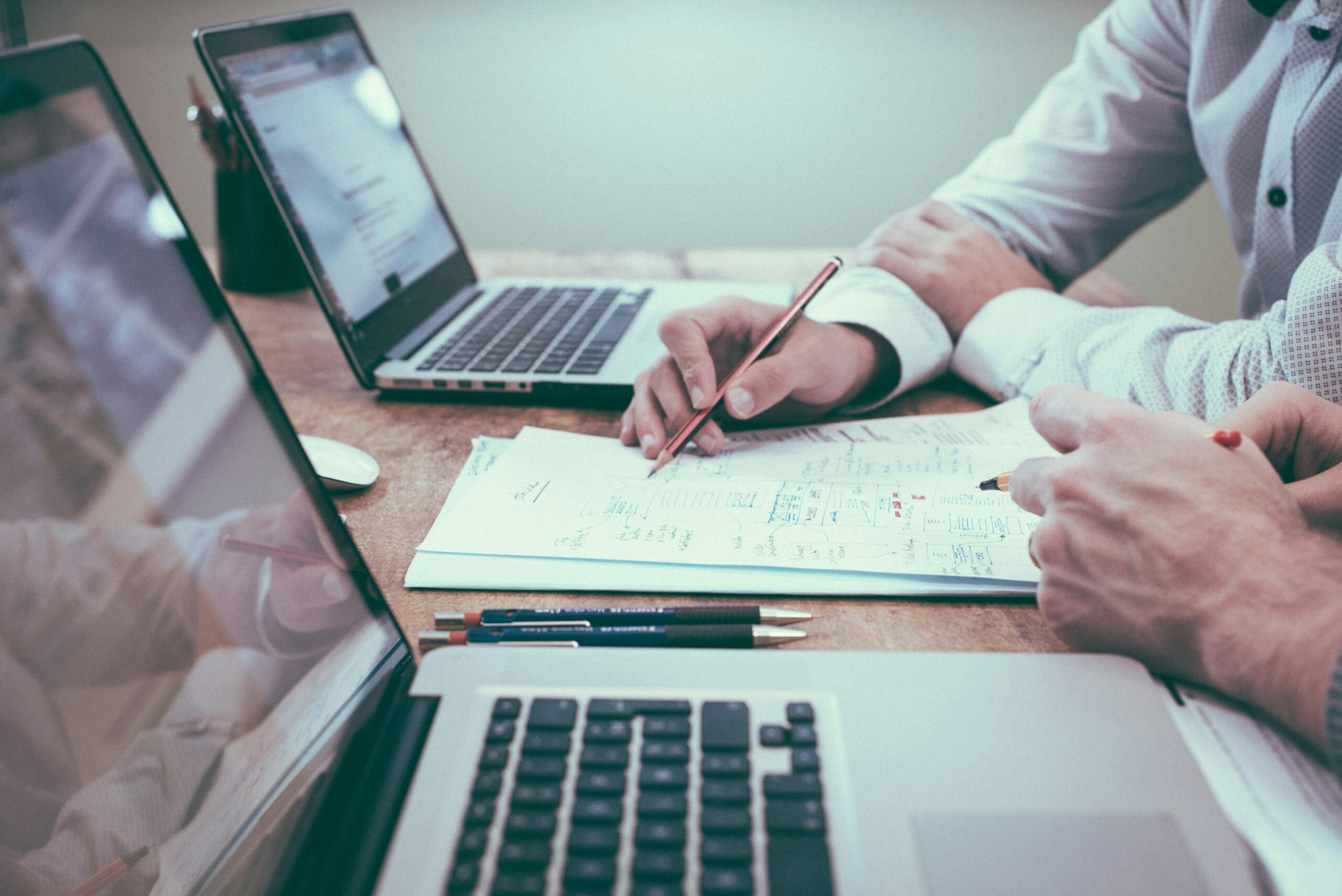
Efficient stock management is essential to the smooth running of a business. It helps to rationalise the layout of the stockroom, control costs and forecast sales. In short, it contributes to customer satisfaction and ensures the long-term future of the business. But do you know what exactly these stocks are that need to be managed? This article will give you a clearer idea of the different types of stock, based on their function, so that you'll be better equipped to put in place an effective stock management strategy.
What is stock?
Stock consists of all incoming goods that are intended to be sold as is or after processing. These goods are held by the company and are generally stored in a warehouse.
They can be of different types: finished products ready for sale, raw materials, maintenance and tools for workstations, packaging and waste.
It is important to know the levels of each in order to avoid imbalances, i.e. stock-outs or, on the contrary, overstocking. To do this, you need to define thresholds, which we will list below.
Safety stock
A buffer stock, or safety stock, is the minimum quantity of a product that you need to have on hand to deal with a delay on the part of your supplier or in exceptional circumstances.
What is the formula for determining it?
Safety stock = Average sale x number of safety days or Safety stock: Maximum sale per day x Maximum supplier lead time per day - Average sale per day x Average replenishment lead time per day |
How do you define safety stock?
Alert stock is used to avoid stock-outs, so plan for a fairly high number. You'll probably feel your way around at first, but you can adjust the level as sales and your supplier's replenishment habits dictate. You will need to determine the average sale per day, the maximum sale per day, the average delivery time and the maximum delivery time. For large sales volumes, other more complex calculation systems exist, such as Gauss's law.
However, it is also important not to plan for too large a quantity of goods, as this could lead to overstocking and a consequent loss of profitability (storage costs, tied-up capital and possible spoilage of foodstuffs). Pareto's law (80/20) can help you choose the types of items that require particular attention when it comes to safety stock quantities: the 20% that generate 80% of sales.
Alert stock
Alert stock, or critical stock, is used to warn you or automatically trigger an order for goods when the quantity reaches a minimum threshold.
What is the formula for determining this?
Alert stock = Minimum stock Safety stock |
How do you define alert stock?
Alert stock is defined :
- By taking into account suppliers' supply and delivery times.
- By considering the quantity of goods needed to satisfy consumers during this period, i.e. average sales. This implies knowing their needs, which is made possible by market research and analysis of previous sales.
Seasonal stock
Some items are more popular or only sell at certain times of the year: winter, summer, holidays, etc. For these, you need to keep a seasonal stock. For these, a specific stock must be kept.
How do you define alert stock?
Alert stock can be managed in two ways:
- Save a replenishment date and a specific stock at the time of peak demand to avoid the cost of stocking up for the rest of the year. You can then plan promotions to sell off unsold stock.
- Take advantage of out-of-season prices to order products and leave them on standby in your stockroom or in rented premises until the right period. Stock rotation should be considered if several of your products are seasonal.
To choose one of these two solutions, you need to calculate which is the most cost-effective, based on supplier offers and storage costs. In any case, as with other types of stock, it is essential to forecast demand by analysing previous sales or those of competitors.
Transit stock
Stock in transit, as its name suggests, is that :
- in production by the manufacturer, being prepared by the supplier or being transported by the carrier to your premises.
- being prepared at your premises for delivery to the customer (in the case of a drive-through, for example) or for delivery.
Knowing the stock of items in transit in real time helps you :
- control your stock: it must be deducted from the actual physical stock in your warehouse, but taken into account as far as costs are concerned (items already settled with the supplier or customer payment already received);
- inform the customer of the progress of the delivery;
- to ask the supplier for explanations about the delivery if there is a delay.
Examining stock in transit can also reveal valuable information, such as recurring problems with delivery companies, which can lead to contracts being revised; the cost of certain modes of transport (boat, plane or other) is too high; or there is too much pollution, which can be resolved by optimising transport.
Speculative inventory
Speculative stock is a set of references that you own :
- following a discount from your supplier ;
- in anticipation of an increase in your supplier's prices or inflation;
- in anticipation of unusual demand;
- by speculating on a higher future value for the items.
It is therefore an unusually large stock compared with ordinary safety stock. It can be linked to seasonal stock. On the other hand, it can lead to storage costs, unsold goods, the tying up of capital or misjudgements. To be as accurate as possible, it is advisable to take into account the nature of your goods (perishable or not, for example), the economic situation and your competitors.
Dormant stock
Dormant stock is also known as dead stock. It refers to items that have not been moved for a given period (usually a year) for a variety of reasons (new standards, loss of appeal, changes in technology, etc.).
Dead stock is problematic because it represents a financial cost in terms of storage, loss of item value and immobilisation of funds. It also takes up space and disrupts warehouse organisation.
It is therefore essential to identify these dormant products by regularly monitoring the stock. Once this has been done, all you have to do is :
- add an alert to your stock management software for slow-moving items;
- improve your forecasts
- decide what to do with unsold products (return to supplier, liquidation, donation, processing, etc.).
You are now familiar with the different types of stock based on their function. By combining these concepts with effective tools for managing and controlling your goods, you will improve your profitability and customer satisfaction. To go even further, particularly to combat shrinkage, which distorts your stock records, you can install an in-store video surveillance system designed to reduce theft. Coupled with cutting-edge technology like our Veesion software, which detects suspicious gestures, you can protect your assets and boost your competitiveness. Contact us for a demonstration and a personalised proposal.
The most popular
Related news
Discover what Veesion can do for you. Do you have one or more stores?
Our team will contact you within 48 hours