What is a stock shortage and how can it be avoided?
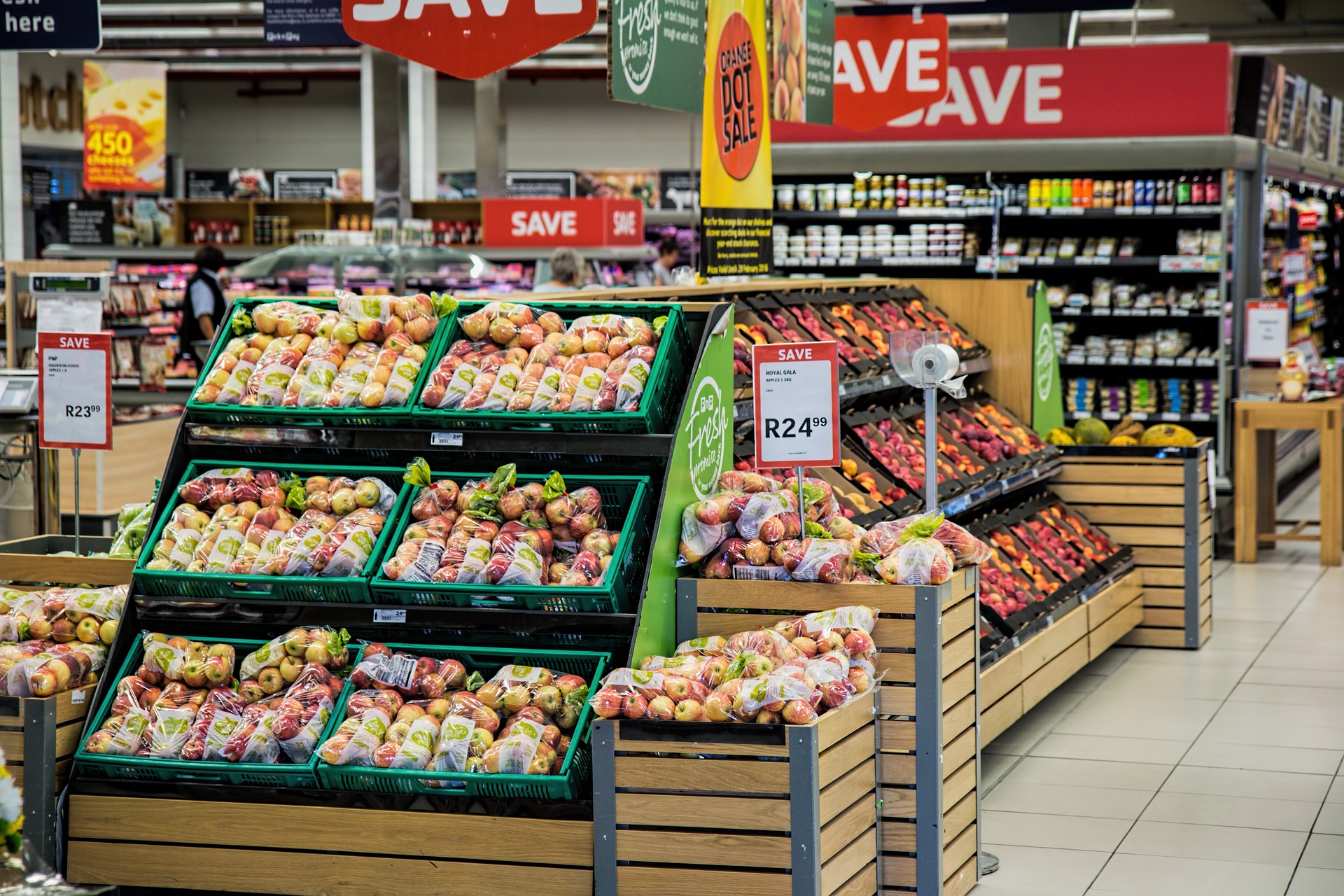
Good stock management is a challenge for all types of business, from grocery stores to pharmacies. You need to have enough of the products you want to avoid stock-outs and keep your customers happy. But how do you go about it?
Types of stock shortages
There are two categories of stock shortages: temporary and permanent. Sometimes demand suddenly explodes due to unforeseen circumstances. Production or delivery can then no longer keep up. But once everything has been fine-tuned, it quickly returns to normal: this is the temporary stock shortage. This was the case, for example, with toilet paper at the start of the Covid 19 crisis.
On the other hand, a permanent stock shortage can have more serious consequences, such as when the product is no longer manufactured because of a shortage of raw materials or a recurring technical problem.
The challenges of stock shortages
In the short term, an out-of-stock situation, whether temporary or permanent, represents a loss of sales. But it can also lead to consumer frustration and even dissatisfaction. Reputation, reliability and therefore brand image are all affected. At best, the customers in question may decide to wait for restocking; at worst, they may turn away from your store and choose the competition.
The cost of being out of stock can be calculated by taking into account the loss of sales themselves and, more indirectly, the loss of customers, as well as the cost of an emergency purchase from another supplier who does not apply the usual prices.
In view of the negative consequences of a stock shortage, it is essential to list the possible causes so that you can be as prepared as possible for unforeseen circumstances.
The causes of stock shortages
As we have seen, stock-outs can be caused by manufacturers or suppliers (damaged products, manufacturing or packaging problems, processing, late delivery or preparation, etc.).
But they can also be caused by your company
- Poor estimation of demand, which has led you to order too few items
- Poor stock organisation (the item was not found or was confused with another)
- Human inventory error (wrong quantity recorded)
- Product damaged on your premises
- Item stolen by a customer or member of staff
Once these causes have been determined, what can you do to prevent stock-outs?
Tools for good stock management
One of the most common solutions is to equip yourself with a stock management tool. Its main advantage is that it centralises all your product data and allows you to customise and automate certain actions, such as :
- Forecasting demand by analysing past sales
- Real-time monitoring of quantities
- Setting up alerts when stock is too low
- Triggering orders with suppliers
- Tracking products from the time they are ordered from the supplier until they are sold
- Extracting and studying retail KPIs (key performance indicators) to identify problems and measure the effectiveness of previous decisions
These tools can be integrated with your IT systems to meet the specific needs of your type of business.
Optimisation through artificial intelligence
Stock management tools can also be boosted with artificial intelligence to improve their efficiency. Artificial intelligence can
- Analyse large quantities of in-depth data: sales history, average delivery times from suppliers, product seasonality, etc.
- Adjust stock levels according to variations, trends or even current events that could affect demand
- Identify a problem, such as an inconsistent number entered during an inventory
- Help you make the right decisions, taking into account planned promotions and possible supplier shortages
This saves you time and money. This applies not only to out-of-stock situations, but also to all the activities involved in managing your stock.
Some department stores even carry out automated stocktaking using robots. These robots pass through the warehouse shelves, read the labels autonomously and update the quantities.
Combating theft
Another method of limiting stock problems is the fight against shrinkage, i.e. the difference between actual stock (physical stock) and theoretical stock. Why this difference? Mainly because of theft by employees or customers, deterioration of items or their expiry date.
By installing video surveillance systems for supermarkets or other stores, you can detect theft and track products. What's more, if you link them to intelligent software for detecting suspicious gestures, such as Veesion, you can increase their effectiveness.
Setting stock levels
To avoid stock-outs, it is also essential to set stock levels:
- The minimum stock level, as its name suggests, is the one that will enable you to meet your needs
- Safety stock, on the other hand, is particularly useful for dealing with the unexpected. Depending on the variability of demand and supplier lead times, you should plan for a back-up quantity in case of fluctuations
- Alert stock tells you when it's time to place an order with your supplier, or does it for you
- Stock in transit lets you know what has been ordered but is not yet in your warehouse. If there is a delay, you can inform the customer and contact the supplier for more details about the lead time
The supplier is a major player in stock management. This is why your relationship with them must be close and transparent
Relations with the supplier
Predicting stock shortages starts with the choice of your suppliers. Suppliers must be reliable by:
- Being transparent about the origin of the products and the manufacturing processes, which gives you an idea of the delays that may occur
- Being available when you need to ask them questions
- Keeping you informed as soon as a problem occurs
- Informing you of changes in demand based on feedback from other customers and the release of new products
- Sharing their stock management data
- Helping you to find solutions in the event of shortages
In addition, don't hesitate to look for back-up suppliers.
Customer relations
In certain circumstances, you can't avoid a breakdown. But you can limit the consequences for your customers. How can you do this? By keeping them informed of the shortage as soon as possible, by trying to find another way of satisfying them (restocking with another supplier, creating a credit note if an order is in progress, refund, etc.) and by being transparent about the reasons for the shortage.
Finally, although stock-outs are common phenomena that cannot be entirely avoided, it is necessary to try to control them and plan solutions upstream. Management software, setting stock levels, analysing KPIs, talking to suppliers and video surveillance systems are all practices that can be put in place.
At Veesion, we help you to combat shrinkage with our software, which detects suspicious gestures and sends you an immediate notification. This gives you the opportunity to take immediate action. If you'd like to find out more, please contact us, we'll find the right solution for your business.
The most popular
Related news
Discover what Veesion can do for you. Do you have one or more stores?
Our team will contact you within 48 hours